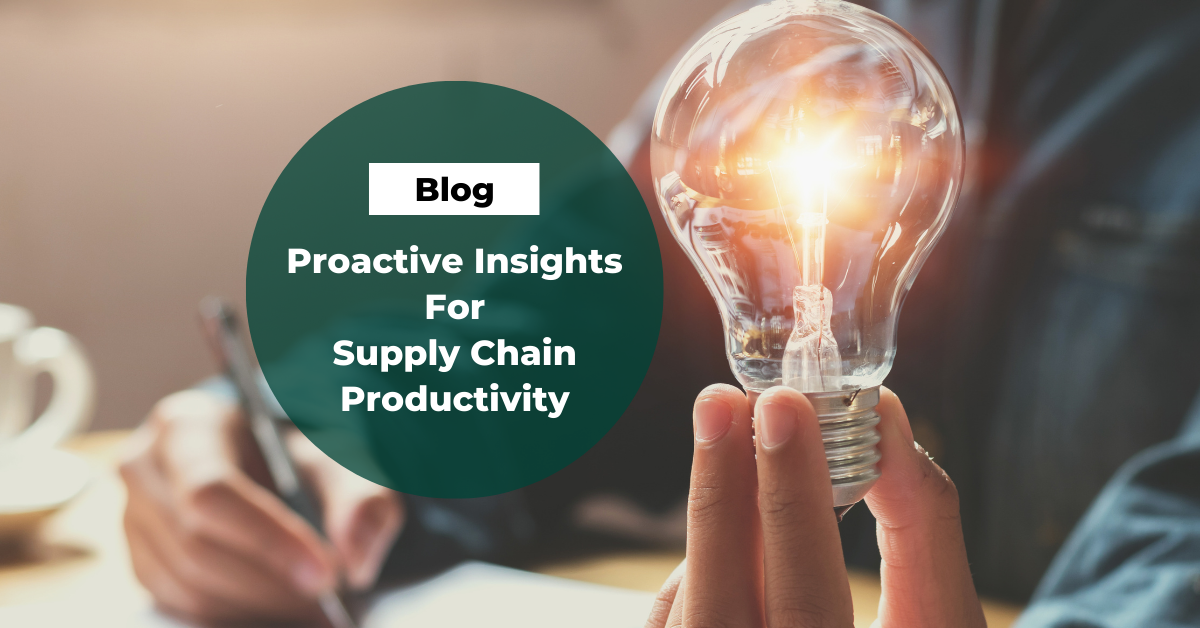
Conversational artificial intelligence (AI) is changing the way people interact with technology. It takes natural language processing and allows enterprises to create advanced dialogue systems that utilize memory, personal preferences and contextual understanding to deliver a realistic and engaging conversation with data sets.
The logistics world uses massive amounts of customer data that changes daily, requiring a great amount of inter-team coordination and organized workflows. The end-to-end process of inputting, tracking and completing orders is time consuming, laborious and vulnerable to human error. So, as distributors continue to incorporate smart systems that leverage artificial intelligence and machine learning, they are depending more on automated assistants to get the job done.
Here are the top 5 ways conversational AI is transforming supply chain operation:
Automates Repetitive Tasks
Conversational AI removes the complex user interface to enable users to engage with technology in a human-like contextual conversation. As a result, the user gets personalized responses to their queries. Layered into this streamlined interaction with data is the added ability to uncover valuable insights within seconds. Automated reports and checklist take the laborious steps and research out of recurring report generation, saving minutes and hours for users on a daily basis.
Improves Workflows Between Users
Conversational AI makes communication between teams and customers a seamless experience. The user simply asks a question and receives insights based on context and keywords. This automated interaction shaves significant time off of the order process from start to finish. By making data easily accessible to various roles within the supply chain hierarchy, data can easily be manipulated and analyzed at any given time.
Acts As A Data Watchdog
AI does the back-end work for supply chain that historically requires several teams and a sharp eye on inventory tracking. The predictive element of conversational AI delivers alerts on errors or anomalies found in inventory. In cases of delay in delivery and incidents, teams receive alerts and act instantly, saving valuable time and resources before an error grows and begins to impact other areas of the supply chain.
Increases Visibility Into Inventory
In logistics, visibility into all stages of an order are of utmost importance. AI is creating more visibility than ever into inventory on hand, turnover and velocity. Predictive monitoring on cycle time and age of inventory is also saving several steps and takes the guessing out of ordering. With the added conversational abilities, actions are completed through natural language or voice commands making real-time updates on products readily available.
Reduces Quality Issues and Increases Customer Satisfaction
With increased visibility comes the ability to prevent small errors or quality issues from turning into large problems that impact customer satisfaction. Product managers can leverage AI for end-to-end inventory management and demand schedules can be proactively predicted to make sure that resources are allocated efficiently. Teams can manage sales orders from start to finish while seeing accurate and correct quantities to meet quality and compliance expectations.
As conversational AI and other emerging technologies are integrated into supply chain and distribution operations, all aspects of the supply chain will evolve to users interacting with technology like they would with a human. The result is an added ability to find answers from multiple complex data sets in real-time, allowing valuable resources to be spent in higher revenue generating functions of the enterprise.
To discover how your supply chain business can improve productivity and efficiency through automation, watch this video or contact [email protected] for a free trial today!