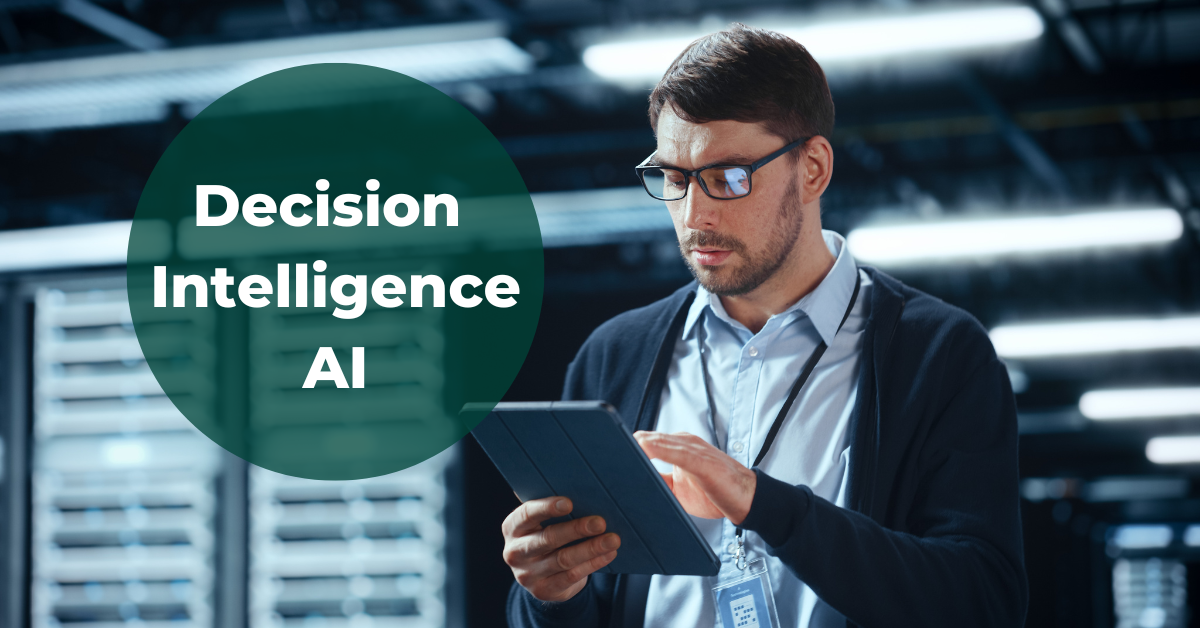
Introduction
In today’s fast-paced manufacturing and supply chain environment, enterprise resource planning (ERP) systems are essential to operational efficiency. And while platforms like Acumatica Cloud ERP offer powerful tools for inventory and process management, ConverSight enhances these capabilities with AI-powered analytics, automation, and real-time decision intelligence.
As a proud technology partner of Acumatica, ConverSight integrates directly with Acumatica ERP to simplify data access, automate workflows, and deliver contextual, predictive insights. Our combined solution empowers manufacturers and distributors to move beyond static dashboards—unlocking the full potential of their inventory data.
In this article, we’ll explore Acumatica’s inventory management capabilities, and show how ConverSight builds on that foundation to make reporting, forecasting, and operational decision-making easier and more impactful.
Now more than ever, having an ERP is paramount to getting accurate visibility into all processes involved in Manufacturing. ERP’s lie at the forefront of Manufacturing and Supply Chain organizations, improving efficiencies and streamlining processes. Central to ERP processes is integrating disparate data systems for data science and other processes to be performed, and ultimately lead to AI and other algorithms reading the data for data insights.
With the rise of cloud technology, businesses are increasingly turning to enterprise resource planning (ERP) systems to streamline operations, and Acumatica Cloud ERP stands out as a powerful solution for inventory management. This blog will explore Acumatica’s capabilities in inventory management, how to generate reports, and how to customize your inventory setup to meet your business needs.
In this article:
- What is Acumatica Cloud ERP?
- Does Acumatica Offer Inventory Management?
- How do I report on Inventory in Acumatica?
- Is there an Acumatica Report that shows all Inventory?
- How to add Custom Fields to Inventory Lookup
What is Acumatica Cloud ERP?
Acumatica Cloud ERP is an integrated business management platform designed to help organizations manage their operations more efficiently. Built on a cloud-first architecture, Acumatica offers a range of modules to handle everything from financial management to manufacturing, distribution, and customer relationship management (CRM).
One of the core modules within Acumatica is Inventory Management—a feature-rich toolkit for tracking stock, managing warehouses, handling order flows, and aligning with accounting processes. When ConverSight is layered into this workflow, teams gain instant access to their inventory insights through interactive dashboards, voice-enabled reports, and predictive models—all powered by AI.
Unlike traditional on-premise solutions, Acumatica’s cloud-based infrastructure allows businesses to access real-time data from anywhere, at any time, using any device. This flexibility, combined with the system’s robust features, makes it an attractive option for companies of all sizes, especially those looking to modernize their operations.
Acumatica’s ERP system is modular, meaning businesses can choose the features they need and scale up as their requirements grow. Inventory management is one of the core modules of Acumatica, providing companies with a comprehensive suite of tools to track and manage their stock efficiently.
See more in our webinar with Acumatica: Conversational AI for Better Outcomes:
Watch the Webinar: Instant, Proactive Insights for Better Outcomes with Acumatic and Conversight
Does Acumatica Offer Inventory Management?
Yes, Acumatica offers a powerful inventory management module that enables businesses to streamline their supply chain processes, optimize stock levels, and improve the overall efficiency of their operations. The inventory management features in Acumatica are designed to cater to a wide range of industries, from retail and wholesale distribution to manufacturing and e-commerce.
Here are some of the key features of Acumatica Inventory Management:
- Real-Time Inventory Tracking: Acumatica allows users to track inventory in real-time, ensuring that your business always knows exactly how much stock is available.
- Location Management: users are able to access analytics on multiple warehouses at the same time, as well as defining location defaults for receiving, returns, and shipping.
- Inventory Valuation: Acumatica supports various inventory valuation methods, including FIFO (First-In-First-Out), LIFO (Last-In-First-Out), and Average Cost.
- Replenishment Methods: users can define min/max quantities, reorder points, seasonality, trends, and more to accurately stock.
- Traceability: users can track inventory by lot or serial number, as well as define shelf life for perishable inventory.
- Integrated Processes: users can get instant financial reporting to improve purchasing, sales, projects, field service, and manufacturing with automation and scheduled tasks, as well as custom workflows.
- Two-Step Receipt Verification: users can implement a two-step verification process for inventory receipts, allowing for greater control over item quantities and product quality.
- Integration with Other Acumatica Modules: Acumatica’s inventory management system is fully integrated with other modules such as sales, purchasing, accounting, and manufacturing. This integration ensures that inventory transactions are automatically reflected across the entire system, reducing the need for manual data entry and minimizing the risk of errors.
Acumatica is not without its pitfalls, as users have reported struggling with:
- Drilling down into data: Acumatica users have reported struggling with drilling down into their integrated data, for more detailed analytics and insights. This can lead to manual, time-consuming tasks for drilling down into data.
- Custom Fields: Pulling custom fields into Acumatica can be a challenge, as custom ERP processes in warehouses can be difficult to navigate.
- Acumatica Generic Inquiries (GI’s): Acumatica GI’s can be slow and cumbersome; paired with custom developments and frameworks, it can get tricky to get accurate insights.
- Limited UI: Acumatica’s UI is limited, and users have reported difficulty in accessing certain functions or finding them amongst various menus and sections of the dashboard.
- Sales and other Real-Time Reporting: Acumatica users have reported struggling with on-demand reporting for warehouse workers and truck drivers fulfilling sales orders.
With ConverSight integrated, users can pull up reports using natural language (e.g., “Show me inventory levels by warehouse”), visualize trends instantly, and automate repetitive tasks like reorder recommendations.
Additional Resources: Acumatica Customization Guide
How do I report on Inventory in Acumatica?
Reporting is one of the most critical aspects of effective inventory management, and Acumatica provides a wide range of reporting tools that allow you to gain insights into your inventory data.
Acumatica has capabilities to generate reports based on user role and permissions, making it easy for users to digest reports and share with third party stakeholders. Real-time dashboards make it easy for users to get real-time insights into their data for easy decision-making.
Let’s explore the different types of Inventory Reports in Acumatica:
1. Inventory Status Report
The Inventory Status Report provides a snapshot of the current inventory levels, showing how much stock is available by item, warehouse, and location. This report helps managers monitor stock levels, track backordered items, and identify products that may be understocked or overstocked.
2. Inventory Valuation Reports
Acumatica supports several inventory valuation reports that allow you to assess the total value of your stock based on the valuation method chosen (FIFO, LIFO, or Average Cost). These reports are essential for financial accounting, as they help ensure your balance sheet accurately reflects the value of your inventory.
3. Stock Transaction History Report
The Stock Transaction History Report tracks all movements of inventory, including purchases, sales, returns, adjustments, and transfers. This detailed report helps businesses maintain accurate records for audit purposes and provides visibility into how inventory levels have changed over time.
4. Inventory Turnover Report
This report calculates how often your inventory is sold and replaced during a given period. It provides a critical measure of inventory efficiency and can help businesses identify slow-moving items, which can be discounted or removed from inventory to free up working capital.
5. Sales Demand and Forecasting Reports
Acumatica’s sales demand and forecasting tools can generate reports that predict future inventory needs based on historical sales data. These reports are invaluable for businesses looking to optimize their stock levels and plan for seasonal or market-driven changes in demand.
6. Custom Reports and Dashboards
One of the key benefits of Acumatica is its flexibility in creating custom reports. Using the built-in report designer, you can create custom inventory reports tailored to your specific business needs. These reports can be saved, scheduled, and shared with other team members to provide insights on inventory performance.
Acumatica’s dashboard capabilities also enable users to create visual reports and KPIs that provide real-time insights into inventory levels, order statuses, and trends. These can be used to proactively address any inventory issues before they become major problems.
How to Supercharge Inventory Reporting in Acumatica
Improving your reporting on inventory in Acumatica using ConverSight involves leveraging the advanced analytics and visualization capabilities of ConverSight to enhance decision-making, streamline processes, and gain deeper insights into your inventory data. Here are several strategies to improve your inventory reporting with ConverSight:
1. Use Real-Time Data for Accurate Reporting
ConverSight integrates with Acumatica and pulls in real-time data, which ensures that your inventory reports are up-to-date. This eliminates the need for manual updates or relying on outdated spreadsheets.
- Action: Set up ConverSight to display live inventory data directly from Acumatica so you can make informed decisions about stock levels, orders, and demand.
2. Create Custom Dashboards for Inventory Insights
ConverSight allows you to create custom dashboards tailored to your specific inventory needs. These dashboards can display key performance indicators (KPIs) such as stock levels, order quantities, aging inventory, and more.
- Action: Design inventory-specific dashboards that reflect the most important metrics like:
- Current Stock Levels: Visual charts or graphs showing quantities by item or location.
- Inventory Turnover: Track how quickly items are sold and replaced.
- Stock Valuation: Visualize the total value of inventory based on real-time cost data.
- Order Trends: Monitor incoming orders and stock-outs to ensure optimal stock levels.
3. Use AI and Machine Learning for Forecasting
ConverSight uses AI and machine learning algorithms to provide predictive analytics for inventory needs. This helps you anticipate demand fluctuations and adjust inventory levels accordingly.
- Action: Use ConverSight’s forecasting features to predict future demand based on historical sales data, seasonal trends, and other external factors. This can help you avoid both overstocking and stockouts.
4. Set Alerts and Notifications
Setting up alerts in ConverSight can help you proactively manage inventory by notifying you when stock levels fall below a certain threshold, when inventory is aging, or when there are any discrepancies.
- Action: Configure automated notifications for:
- Low Stock: Alerts for items that are running low and need reordering.
- Slow-Moving Inventory: Alerts for products that have been sitting in stock for a long time.
- Backordered Items: Notifications when a backorder is due for fulfillment.
5. Analyze Inventory Trends with Interactive Reporting
Use ConverSight’s interactive reporting capabilities to drill down into inventory trends over time, understand seasonal demand, and identify any supply chain inefficiencies.
- Action: Create visual reports showing historical inventory data, order fulfillment rates, and vendor performance. This can highlight opportunities to optimize purchasing or streamline warehousing.
6. Drill Down into Inventory Details
ConverSight allows you to easily drill down into specific items or categories to analyze their performance in detail. This can help you understand which products are driving inventory costs and which are underperforming.
- Action: Use the drill-down feature to analyze:
- Individual item sales performance.
- Historical inventory fluctuations for each SKU.
- Product lifecycle data to make informed decisions about discontinuing or reordering products.
7. Track Multiple Locations and Warehouses
If your business has inventory spread across different warehouses or locations, ConverSight can provide a consolidated view of stock across all sites, allowing for better cross-location management and efficient stock transfers.
- Action: Set up reports to track inventory across different locations and warehouses. This can help you optimize stock allocation and quickly identify where a product is overstocked or understocked.
8. Integrate Supplier and Vendor Data
Inventory management is not just about what you have in stock but also about how quickly you can replenish. ConverSight can integrate vendor and supplier data, helping you better understand lead times and order cycles.
- Action: Create a report showing supplier lead times, reorder points, and historical supplier performance to ensure your inventory is always stocked in a timely manner.
9. Simplify Decision-Making with Natural Language Queries
ConverSight offers natural language query capabilities, so you can simply ask questions about your inventory in plain language (e.g., “What is the current stock level of product X?” or “Which items have been in stock for over 90 days?”).
- Action: Train your team to use natural language queries to retrieve inventory reports quickly without having to navigate through multiple screens or filters.
10. Leverage Mobile Reporting for On-the-Go Access
If your team needs to access inventory reports on-the-go, ConverSight offers mobile-friendly dashboards and reports. This is ideal for warehouse managers or field teams who need instant access to inventory insights.
- Action: Set up mobile access to inventory reports and alerts for warehouse managers to monitor inventory levels, track shipments, or check stock availability while in the field.
Using AI For Inventory Management in Acumatica
Here’s how you can harness the power of AI to enhance inventory management in Acumatica:
1. AI-Powered Demand Forecasting
One of the most impactful uses of AI in inventory management is demand forecasting. Traditional methods often rely on historical data and static formulas, but AI can take this further by analyzing large datasets and identifying patterns that might not be visible to the human eye.
- How it works in Acumatica:
- AI can analyze past sales trends, seasonal demand, promotions, and external factors (e.g., weather, economic data) to predict future demand.
- These predictions can help you avoid overstocking or understocking by adjusting your orders based on future needs rather than just historical trends.
- Action:
- Integrate an AI forecasting tool into Acumatica, or use Acumatica’s built-in features (like the Forecasting module in Acumatica Distribution or Manufacturing) enhanced with AI-driven data models.
- Enable automated stock level adjustments and purchase orders based on these forecasts, ensuring you have the right amount of stock at the right time.
2. AI-Driven Inventory Optimization
AI can assist in inventory optimization by continuously analyzing inventory levels, turnover rates, and sales trends to recommend the ideal stock levels for each SKU (Stock Keeping Unit).
- How it works in Acumatica:
- AI algorithms analyze historical sales patterns and adjust reorder points, safety stock levels, and economic order quantities (EOQ) to ensure you are neither overstocking nor understocking inventory.
- The system will take into account various factors such as lead time from suppliers, stock turnover, and seasonal fluctuations.
- Action:
- Leverage AI algorithms to create optimized replenishment strategies based on real-time demand and supplier lead times.
- Use AI tools like ConverSight for real-time insights and inventory recommendations or integrate AI-based third-party add-ons into Acumatica.
3. Automated Stock Replenishment
AI can be used to automate stock replenishment based on forecasted demand and current inventory levels. Instead of manually monitoring stock levels and placing purchase orders, AI systems can automatically trigger orders when stocks fall below a defined threshold.
- How it works in Acumatica:
- AI analyzes historical usage data and forecasts future demand to automate purchase orders and restocking processes.
- The AI system can take into account factors such as supplier lead times, transportation delays, and any historical disruptions (e.g., delays or stock-outs) to adjust reorder schedules.
- Action:
- Set up automated purchasing workflows in Acumatica that are driven by AI-generated demand forecasts, ensuring that your inventory is always optimally stocked.
- Integrate AI-based solutions (like machine learning-based forecasting) with your Acumatica Procurement module.
4. AI for Supplier Performance Analysis
AI can analyze supplier performance data over time, helping you assess the reliability, lead time, and order fulfillment accuracy of each supplier. This analysis can be used to improve decision-making when choosing suppliers or renegotiating terms.
- How it works in Acumatica:
- AI can aggregate data from past purchase orders, deliveries, and performance metrics to generate insights about which suppliers consistently meet delivery times, quality standards, and cost expectations.
- Action:
- Implement AI-based analytics within Acumatica’s Vendor Management module to evaluate supplier performance. Use this data to streamline your supplier selection process, optimize lead times, and potentially negotiate better contracts based on data-backed insights.
5. AI-Powered Inventory Audits and Cycle Counting
Conducting physical inventory audits or cycle counts is often time-consuming and prone to human error. AI can enhance the cycle counting process by analyzing historical data to predict when certain items are more likely to be out of place or incorrectly counted.
- How it works in Acumatica:
- AI can be used to predict inventory discrepancies by comparing actual stock levels with historical data, helping to identify potential areas for audit.
- The system can prioritize inventory counts for high-turnover items, items with a history of discrepancies, or critical products based on AI-driven risk assessments.
- Action:
- Use AI-powered cycle counting tools to automate inventory audits. Incorporate machine learning models that can suggest the frequency and focus areas for cycle counting within Acumatica.
- Implement RFID or barcode scanning technologies in conjunction with AI to track inventory and reduce human error in counting.
6. Predicting Stockouts and Overstock Situations
AI can help predict stockouts before they happen by analyzing trends such as customer demand, current inventory levels, and supplier performance. Similarly, AI can also identify products that are at risk of overstocking.
- How it works in Acumatica:
- By incorporating AI into Acumatica’s Inventory Management module, the system will use historical sales patterns, supplier lead times, and seasonality to predict when stock levels will drop below minimum thresholds.
- AI algorithms can automatically raise alerts or even trigger reordering processes when stock levels are predicted to hit critical levels.
- Action:
- Set up AI-driven alerts in Acumatica for items that are at risk of stockouts or overstocking.
- Use AI-powered recommendations for adjusting reorder points based on real-time data and predictive analytics.
7. AI-Powered Supplier and Demand Matching
AI can help match your suppliers with the right demand forecast and optimize order quantities to meet demand without over-ordering or under-ordering.
- How it works in Acumatica:
- By integrating AI-driven forecasting and supplier lead time data into Acumatica, AI can recommend the most efficient ordering strategy for each supplier, ensuring timely deliveries and optimal stock levels.
- Action:
- Enable automated supplier demand matching within Acumatica to ensure that inventory levels are always aligned with the most accurate forecasts.
8. AI for Identifying and Managing Slow-Moving Inventory
AI can help identify products that are slow-moving or dead stock, allowing businesses to take corrective actions like promotions or discounts to clear out stock.
- How it works in Acumatica:
- AI algorithms can track sales velocity and compare it against stock levels to identify products that are not selling as expected.
- The AI can generate reports on slow-moving items, propose sales strategies, or recommend liquidation methods to reduce excess inventory.
- Action:
- Set up AI-powered slow-moving inventory alerts within Acumatica and use the AI suggestions to make decisions about discounting, bundle offers, or removing items from your inventory.
Video: Report Creation in Acumatica (Platform video)
Is there an Acumatica Report that shows all Inventory?
Yes, Acumatica offers several reports that give a comprehensive overview of all inventory items across your entire system. Some of the most useful reports for showing all inventory include:
1. Inventory Item List
The Inventory Item List report is a basic yet effective report that shows all the inventory items in your system, along with key details such as item codes, descriptions, quantities on hand, and stock values. This report is helpful for a quick overview of your entire inventory.
2. Inventory Transactions Report
The Inventory Transactions Report shows all transactions that have affected inventory levels, including purchases, sales, transfers, and adjustments. This report provides a detailed view of inventory movement, which is essential for understanding inventory activity over a specific period.
3. Inventory Valuation Report
This report displays all inventory items and their corresponding values, based on your selected inventory valuation method. The report shows the total value of your stock, as well as how that value has changed over time, which is particularly useful for financial analysis.
4. Inventory Aging Report
The Inventory Aging Report categorizes inventory by the length of time it has been in stock. This report can help you identify slow-moving items that may need to be discounted, promoted, or removed from your inventory.
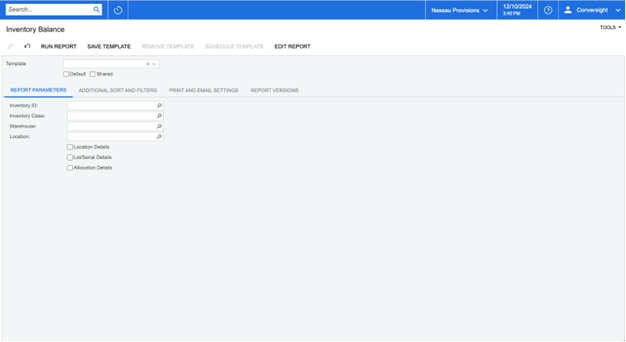
Automated Reporting with ConverSight
Automating inventory management in Acumatica with ConverSight can significantly enhance efficiency, streamline operations, and reduce human error. ConverSight, with its AI-powered analytics and integration capabilities, offers tools that can automate many aspects of inventory management in Acumatica, including stock tracking, demand forecasting, order management, and supplier coordination.
1. Integrate ConverSight with Acumatica
Before automating inventory management, ensure that ConverSight is properly integrated with Acumatica. This allows for real-time data exchange between the two systems, ensuring that inventory data, orders, sales, and other metrics are continuously updated.
- Action:
- Work with your IT team or Acumatica partner to establish an integration between Acumatica and ConverSight.
- Ensure that relevant data fields such as inventory levels, sales orders, purchase orders, and supplier data are synchronized.
2. Automate Inventory Forecasting and Demand Planning
AI-powered demand forecasting is one of the key features that ConverSight offers to automate inventory management. Using historical sales data and advanced machine learning models, ConverSight can predict future demand, allowing you to adjust stock levels proactively.
- Action:
- Configure ConverSight’s demand forecasting tool to analyze historical sales data and generate accurate demand predictions.
- Set up automated reorder points in Acumatica based on these predictions so that the system automatically places orders when stock levels reach a threshold.
- Adjust safety stock levels based on forecast data to avoid stockouts or overstocking.
Benefits:
- Accurate forecasts based on historical data, seasonality, and trends.
- Proactive inventory replenishment to reduce manual intervention.
3. Automate Stock Replenishment
Once you have forecasted demand, you can automate the process of stock replenishment. ConverSight can recommend when and how much inventory should be ordered based on real-time analytics.
- Action:
- Use ConverSight’s inventory recommendations to determine when to reorder stock based on demand forecasts and current inventory levels.
- Set up automated purchase orders in Acumatica that are triggered by low inventory or approaching stock-out conditions, based on ConverSight’s recommendations.
- Integrate lead time data for suppliers into the system to automate the replenishment process in a timely manner, ensuring inventory arrives when needed.
Benefits:
- Streamlined ordering process with less manual oversight.
- Reduced risk of stockouts or excess inventory.
4. AI-Powered Supplier Management and Coordination
ConverSight helps optimize supplier relationships by providing insights into supplier performance, delivery times, and order accuracy. By automating this process, you can ensure that you’re always working with the most reliable suppliers and minimize delays.
- Action:
- Analyze supplier data in ConverSight to understand supplier lead times, order fulfillment rates, and performance.
- Use this data to automatically select suppliers for reorder based on their reliability and performance history.
- Automate purchase orders based on the supplier’s lead time and product availability, ensuring timely restocking.
Benefits:
- Improved supplier relationships through data-driven insights.
- Reduced manual oversight of supplier management.
5. Automate Stock Adjustments Based on Real-Time Data
ConverSight can continuously analyze inventory movements in real-time, allowing the system to flag discrepancies or trends that require attention. By integrating this capability with Acumatica, stock adjustments can be automated.
- Action:
- Enable real-time inventory tracking in Acumatica via ConverSight to detect changes in inventory, including stockouts, excess stock, or discrepancies.
- Use AI-driven alerts in ConverSight to notify relevant stakeholders about stock levels that need attention, such as items that are moving too quickly or too slowly.
- Set up automated inventory adjustments in Acumatica, where the system can automatically adjust stock levels based on discrepancies detected by ConverSight.
Benefits:
- Continuous monitoring of inventory for stock discrepancies.
- Faster response times to address any issues or discrepancies.
6. Automate Inventory Reconciliation and Cycle Counting
AI-powered cycle counting and inventory reconciliation can be automated using ConverSight, ensuring that inventory counts are accurate without requiring manual intervention.
- Action:
- Use AI-based insights from ConverSight to prioritize high-value or high-turnover items for cycle counting.
- Set up automated alerts for discrepancies between physical inventory and recorded inventory, so that corrective actions can be taken promptly.
- Automate inventory counts and reconciliations in Acumatica, allowing cycle counts to trigger adjustments automatically.
Benefits:
- Reduced human error during inventory counts.
- Less time spent on manual reconciliation efforts.
7. Optimize Inventory Location and Warehouse Management
If your business operates in multiple locations or warehouses, ConverSight can automate inventory distribution between sites based on demand, stock levels, and warehouse capacity. This ensures efficient stock movement and utilization across the organization.
- Action:
- Use ConverSight’s AI-driven analytics to monitor inventory across multiple warehouses or locations.
- Automatically redistribute stock based on demand, ensuring that high-demand products are always available in the right locations.
- Set up automated stock transfers in Acumatica, triggered by ConverSight’s analysis of inventory levels across different sites.
Benefits:
- Optimized inventory levels across multiple locations.
- Improved warehouse efficiency through automated stock movement.
8. Automate Reporting and Analytics for Inventory Management
ConverSight provides real-time reporting and interactive dashboards that can be automated to generate insights about your inventory management. These reports can be scheduled and automatically sent to key stakeholders.
- Action:
- Set up automated reports in ConverSight that provide insights into key inventory metrics like stock turnover, aging inventory, order trends, and stockouts.
- Schedule these reports to be sent to managers, warehouse teams, and procurement teams at predefined intervals (e.g., daily, weekly, monthly).
- Use interactive dashboards that give stakeholders real-time access to inventory status and recommendations for adjustments.
Benefits:
- Timely, data-driven insights for decision-making.
- Less reliance on manual reporting and data entry.
9. Use ConverSight’s Natural Language Queries for Inventory Insights
One of the unique features of ConverSight is its ability to handle natural language queries, allowing users to ask questions about inventory status, trends, or predictions without needing technical expertise.
- Action:
- Train your team to use natural language queries to retrieve inventory reports quickly (e.g., “What is the current stock level for item X?” or “Which items have been overstocked in the last 30 days?”).
- Use AI-driven insights from these queries to automate restocking or reordering actions within Acumatica.
Benefits:
- Faster access to insights without complex data manipulation.
- Increased efficiency and better decision-making.
10. Implement AI-Powered Alerts for Proactive Inventory Management
Set up AI-driven alerts in ConverSight that notify relevant users when specific inventory thresholds are crossed or when anomalies are detected. This can be an important part of the automation process, as it ensures proactive action before problems arise.
- Action:
- Configure alerts for low stock, high stock, aging inventory, and unfulfilled orders based on AI insights.
- Set up rules for automated replenishment or stock movement based on these alerts.
Benefits:
- Proactive management of inventory.
- Reduced risk of stockouts, overstocking, and waste.
How to add Custom Fields to Inventory Lookup
Acumatica allows users to customize their inventory setup to meet specific business requirements. Adding custom fields to the inventory lookup screen is one such customization that can help businesses track additional information about their inventory items.
1. Navigate to the Customization Menu
To add custom fields, go to the “Customization” menu within Acumatica. From here, select “Customization Projects” to create or modify an existing project.
2. Create a New Customization Project
If you don’t already have a customization project, click “New Project.” Give it a name (e.g., “Inventory Custom Fields”) and select “Add” to start editing the inventory module.
3. Add a New Field to the Inventory Table
In the Customization Project editor, navigate to the Inventory table (usually named InventoryItem). From here, click “Add Field” to create a new custom field. You can choose from various data types (text, date, number, etc.) depending on the kind of information you wish to track.
4. Edit the Inventory Lookup Screen
Next, navigate to the Inventory Lookup screen, where you want the new custom field to appear. In the screen editor, select the area where you want to place the custom field, then drag and drop the newly created field into the desired location.
5. Publish the Customization
Once you’ve added the custom field to the lookup screen, save your changes, and publish the customization. The new field will now be visible on the Inventory Lookup screen, allowing users to enter and view additional data for each inventory item.
6. Testing the Custom Field
After publishing the customization, test the new field by adding data to it in the Inventory Lookup screen. Make sure it functions as expected and integrates with other areas of the system, such as reports or dashboards.
By adding custom fields to the Inventory Lookup screen, you can ensure that Acumatica is tailored to your unique business needs and provides all the information you require to manage
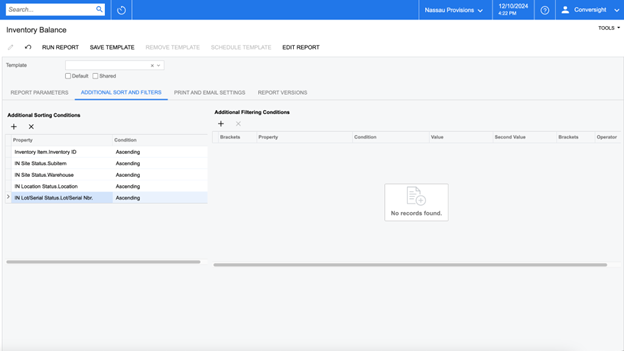
Adding AI-Powered Decision Intelligence to Acumatica
Some top use cases that customers are utilizing in ConverSight include:
- AI-Driven Demand Forecasting: One of the most impactful ways ConverSight can help is by improving demand forecasting. AI-based forecasting tools analyze historical sales data, seasonality, and external factors to predict future demand more accurately.
- ROI: 55% reduction in decision cycle time, 75% reduction in time spent by analysts, 28% reduction in stockouts
- Real-Time Inventory Tracking & Insights: ConverSight provides real-time visibility into your inventory across multiple locations, warehouses, or sales channels. This allows for more precise tracking of stock levels and performance metrics.
- ROI: 40% reduction in time spent creating reports, 18% increase in on-time delivery, 24% reduction in e-commerce order fulfillment costs
- Automate Stock Replenishment: ConverSight uses AI and predictive analytics to automate inventory replenishment based on real-time data and demand forecasts. This can significantly reduce manual oversight and streamline purchasing processes.
- ROI: 12% reduction in PO fulfillment delay, 40% reduction in PO and MO cycle time, 10% decrease in month-to-month costs
Conclusion
Integrating AI and automation into Acumatica ERP can greatly enhance its capabilities, transforming how businesses manage core operations such as inventory, finance, customer service, sales, and supply chain. By leveraging artificial intelligence and automation, Acumatica ERP becomes smarter, more efficient, and proactive in decision-making, allowing companies to stay competitive and agile. ConverSight provides a platform for easily integrating AI and automation into your Acumatica Cloud ERP instance, providing the most optimized and up-to-date insights.
See firsthand how ConverSight can revolutionize your Acumatica instance.
Now more than ever, having an ERP is paramount to getting accurate visibility into all processes involved in Manufacturing. ERP’s lie at the forefront of Manufacturing and Supply Chain organizations, improving efficiencies and streamlining processes. Central to ERP processes is integrating disparate data systems for data science and other processes to be performed, and ultimately lead to AI and other algorithms reading the data for data insights.
With the rise of cloud technology, businesses are increasingly turning to enterprise resource planning (ERP) systems to streamline operations, and Acumatica Cloud ERP stands out as a powerful solution for inventory management. This blog will explore Acumatica’s capabilities in inventory management, how to generate reports, and how to customize your inventory setup to meet your business needs.
In this article:
- What is Acumatica Cloud ERP?
- Does Acumatica Offer Inventory Management?
- How do I report on Inventory in Acumatica?
- Is there an Acumatica Report that shows all Inventory?
- How to add Custom Fields to Inventory Lookup
What is Acumatica Cloud ERP?
Acumatica Cloud ERP is an integrated business management platform designed to help organizations manage their operations more efficiently. Built on a cloud-first architecture, Acumatica offers a range of modules to handle everything from financial management to manufacturing, distribution, and customer relationship management (CRM).
Unlike traditional on-premise solutions, Acumatica’s cloud-based infrastructure allows businesses to access real-time data from anywhere, at any time, using any device. This flexibility, combined with the system’s robust features, makes it an attractive option for companies of all sizes, especially those looking to modernize their operations.
Acumatica’s ERP system is modular, meaning businesses can choose the features they need and scale up as their requirements grow. Inventory management is one of the core modules of Acumatica, providing companies with a comprehensive suite of tools to track and manage their stock efficiently.
See more in our webinar with Acumatica: Conversational AI for Better Outcomes:
Watch the Webinar: Instant, Proactive Insights for Better Outcomes with Acumatic and Conversight
Does Acumatica Offer Inventory Management?
Yes, Acumatica offers a powerful inventory management module that enables businesses to streamline their supply chain processes, optimize stock levels, and improve the overall efficiency of their operations. The inventory management features in Acumatica are designed to cater to a wide range of industries, from retail and wholesale distribution to manufacturing and e-commerce.
Here are some of the key features of Acumatica Inventory Management:
- Real-Time Inventory Tracking: Acumatica allows users to track inventory in real-time, ensuring that your business always knows exactly how much stock is available.
- Location Management: users are able to access analytics on multiple warehouses at the same time, as well as defining location defaults for receiving, returns, and shipping.
- Inventory Valuation: Acumatica supports various inventory valuation methods, including FIFO (First-In-First-Out), LIFO (Last-In-First-Out), and Average Cost.
- Replenishment Methods: users can define min/max quantities, reorder points, seasonality, trends, and more to accurately stock.
- Traceability: users can track inventory by lot or serial number, as well as define shelf life for perishable inventory.
- Integrated Processes: users can get instant financial reporting to improve purchasing, sales, projects, field service, and manufacturing with automation and scheduled tasks, as well as custom workflows.
- Two-Step Receipt Verification: users can implement a two-step verification process for inventory receipts, allowing for greater control over item quantities and product quality.
- Integration with Other Acumatica Modules: Acumatica’s inventory management system is fully integrated with other modules such as sales, purchasing, accounting, and manufacturing. This integration ensures that inventory transactions are automatically reflected across the entire system, reducing the need for manual data entry and minimizing the risk of errors.
Acumatica is not without its pitfalls, as users have reported struggling with:
- Drilling down into data: Acumatica users have reported struggling with drilling down into their integrated data, for more detailed analytics and insights. This can lead to manual, time-consuming tasks for drilling down into data.
- Custom Fields: Pulling custom fields into Acumatica can be a challenge, as custom ERP processes in warehouses can be difficult to navigate.
- Acumatica Generic Inquiries (GI’s): Acumatica GI’s can be slow and cumbersome; paired with custom developments and frameworks, it can get tricky to get accurate insights.
- Limited UI: Acumatica’s UI is limited, and users have reported difficulty in accessing certain functions or finding them amongst various menus and sections of the dashboard.
- Sales and other Real-Time Reporting: Acumatica users have reported struggling with on-demand reporting for warehouse workers and truck drivers fulfilling sales orders.
Additional Resources: Acumatica Customization Guide
How do I report on Inventory in Acumatica?
Reporting is one of the most critical aspects of effective inventory management, and Acumatica provides a wide range of reporting tools that allow you to gain insights into your inventory data.
Acumatica has capabilities to generate reports based on user role and permissions, making it easy for users to digest reports and share with third party stakeholders. Real-time dashboards make it easy for users to get real-time insights into their data for easy decision-making.
Let’s explore the different types of Inventory Reports in Acumatica:
1. Inventory Status Report
The Inventory Status Report provides a snapshot of the current inventory levels, showing how much stock is available by item, warehouse, and location. This report helps managers monitor stock levels, track backordered items, and identify products that may be understocked or overstocked.
2. Inventory Valuation Reports
Acumatica supports several inventory valuation reports that allow you to assess the total value of your stock based on the valuation method chosen (FIFO, LIFO, or Average Cost). These reports are essential for financial accounting, as they help ensure your balance sheet accurately reflects the value of your inventory.
3. Stock Transaction History Report
The Stock Transaction History Report tracks all movements of inventory, including purchases, sales, returns, adjustments, and transfers. This detailed report helps businesses maintain accurate records for audit purposes and provides visibility into how inventory levels have changed over time.
4. Inventory Turnover Report
This report calculates how often your inventory is sold and replaced during a given period. It provides a critical measure of inventory efficiency and can help businesses identify slow-moving items, which can be discounted or removed from inventory to free up working capital.
5. Sales Demand and Forecasting Reports
Acumatica’s sales demand and forecasting tools can generate reports that predict future inventory needs based on historical sales data. These reports are invaluable for businesses looking to optimize their stock levels and plan for seasonal or market-driven changes in demand.
6. Custom Reports and Dashboards
One of the key benefits of Acumatica is its flexibility in creating custom reports. Using the built-in report designer, you can create custom inventory reports tailored to your specific business needs. These reports can be saved, scheduled, and shared with other team members to provide insights on inventory performance.
Acumatica’s dashboard capabilities also enable users to create visual reports and KPIs that provide real-time insights into inventory levels, order statuses, and trends. These can be used to proactively address any inventory issues before they become major problems.
How to Supercharge Inventory Reporting in Acumatica
Improving your reporting on inventory in Acumatica using ConverSight involves leveraging the advanced analytics and visualization capabilities of ConverSight to enhance decision-making, streamline processes, and gain deeper insights into your inventory data. Here are several strategies to improve your inventory reporting with ConverSight:
1. Use Real-Time Data for Accurate Reporting
ConverSight integrates with Acumatica and pulls in real-time data, which ensures that your inventory reports are up-to-date. This eliminates the need for manual updates or relying on outdated spreadsheets.
- Action: Set up ConverSight to display live inventory data directly from Acumatica so you can make informed decisions about stock levels, orders, and demand.
2. Create Custom Dashboards for Inventory Insights
ConverSight allows you to create custom dashboards tailored to your specific inventory needs. These dashboards can display key performance indicators (KPIs) such as stock levels, order quantities, aging inventory, and more.
- Action: Design inventory-specific dashboards that reflect the most important metrics like:
- Current Stock Levels: Visual charts or graphs showing quantities by item or location.
- Inventory Turnover: Track how quickly items are sold and replaced.
- Stock Valuation: Visualize the total value of inventory based on real-time cost data.
- Order Trends: Monitor incoming orders and stock-outs to ensure optimal stock levels.
3. Use AI and Machine Learning for Forecasting
ConverSight uses AI and machine learning algorithms to provide predictive analytics for inventory needs. This helps you anticipate demand fluctuations and adjust inventory levels accordingly.
- Action: Use ConverSight’s forecasting features to predict future demand based on historical sales data, seasonal trends, and other external factors. This can help you avoid both overstocking and stockouts.
4. Set Alerts and Notifications
Setting up alerts in ConverSight can help you proactively manage inventory by notifying you when stock levels fall below a certain threshold, when inventory is aging, or when there are any discrepancies.
- Action: Configure automated notifications for:
- Low Stock: Alerts for items that are running low and need reordering.
- Slow-Moving Inventory: Alerts for products that have been sitting in stock for a long time.
- Backordered Items: Notifications when a backorder is due for fulfillment.
5. Analyze Inventory Trends with Interactive Reporting
Use ConverSight’s interactive reporting capabilities to drill down into inventory trends over time, understand seasonal demand, and identify any supply chain inefficiencies.
- Action: Create visual reports showing historical inventory data, order fulfillment rates, and vendor performance. This can highlight opportunities to optimize purchasing or streamline warehousing.
6. Drill Down into Inventory Details
ConverSight allows you to easily drill down into specific items or categories to analyze their performance in detail. This can help you understand which products are driving inventory costs and which are underperforming.
- Action: Use the drill-down feature to analyze:
- Individual item sales performance.
- Historical inventory fluctuations for each SKU.
- Product lifecycle data to make informed decisions about discontinuing or reordering products.
7. Track Multiple Locations and Warehouses
If your business has inventory spread across different warehouses or locations, ConverSight can provide a consolidated view of stock across all sites, allowing for better cross-location management and efficient stock transfers.
- Action: Set up reports to track inventory across different locations and warehouses. This can help you optimize stock allocation and quickly identify where a product is overstocked or understocked.
8. Integrate Supplier and Vendor Data
Inventory management is not just about what you have in stock but also about how quickly you can replenish. ConverSight can integrate vendor and supplier data, helping you better understand lead times and order cycles.
- Action: Create a report showing supplier lead times, reorder points, and historical supplier performance to ensure your inventory is always stocked in a timely manner.
9. Simplify Decision-Making with Natural Language Queries
ConverSight offers natural language query capabilities, so you can simply ask questions about your inventory in plain language (e.g., “What is the current stock level of product X?” or “Which items have been in stock for over 90 days?”).
- Action: Train your team to use natural language queries to retrieve inventory reports quickly without having to navigate through multiple screens or filters.
10. Leverage Mobile Reporting for On-the-Go Access
If your team needs to access inventory reports on-the-go, ConverSight offers mobile-friendly dashboards and reports. This is ideal for warehouse managers or field teams who need instant access to inventory insights.
- Action: Set up mobile access to inventory reports and alerts for warehouse managers to monitor inventory levels, track shipments, or check stock availability while in the field.
Using AI For Inventory Management in Acumatica
Here’s how you can harness the power of AI to enhance inventory management in Acumatica:
1. AI-Powered Demand Forecasting
One of the most impactful uses of AI in inventory management is demand forecasting. Traditional methods often rely on historical data and static formulas, but AI can take this further by analyzing large datasets and identifying patterns that might not be visible to the human eye.
- How it works in Acumatica:
- AI can analyze past sales trends, seasonal demand, promotions, and external factors (e.g., weather, economic data) to predict future demand.
- These predictions can help you avoid overstocking or understocking by adjusting your orders based on future needs rather than just historical trends.
- Action:
- Integrate an AI forecasting tool into Acumatica, or use Acumatica’s built-in features (like the Forecasting module in Acumatica Distribution or Manufacturing) enhanced with AI-driven data models.
- Enable automated stock level adjustments and purchase orders based on these forecasts, ensuring you have the right amount of stock at the right time.
2. AI-Driven Inventory Optimization
AI can assist in inventory optimization by continuously analyzing inventory levels, turnover rates, and sales trends to recommend the ideal stock levels for each SKU (Stock Keeping Unit).
- How it works in Acumatica:
- AI algorithms analyze historical sales patterns and adjust reorder points, safety stock levels, and economic order quantities (EOQ) to ensure you are neither overstocking nor understocking inventory.
- The system will take into account various factors such as lead time from suppliers, stock turnover, and seasonal fluctuations.
- Action:
- Leverage AI algorithms to create optimized replenishment strategies based on real-time demand and supplier lead times.
- Use AI tools like ConverSight for real-time insights and inventory recommendations or integrate AI-based third-party add-ons into Acumatica.
3. Automated Stock Replenishment
AI can be used to automate stock replenishment based on forecasted demand and current inventory levels. Instead of manually monitoring stock levels and placing purchase orders, AI systems can automatically trigger orders when stocks fall below a defined threshold.
- How it works in Acumatica:
- AI analyzes historical usage data and forecasts future demand to automate purchase orders and restocking processes.
- The AI system can take into account factors such as supplier lead times, transportation delays, and any historical disruptions (e.g., delays or stock-outs) to adjust reorder schedules.
- Action:
- Set up automated purchasing workflows in Acumatica that are driven by AI-generated demand forecasts, ensuring that your inventory is always optimally stocked.
- Integrate AI-based solutions (like machine learning-based forecasting) with your Acumatica Procurement module.
4. AI for Supplier Performance Analysis
AI can analyze supplier performance data over time, helping you assess the reliability, lead time, and order fulfillment accuracy of each supplier. This analysis can be used to improve decision-making when choosing suppliers or renegotiating terms.
- How it works in Acumatica:
- AI can aggregate data from past purchase orders, deliveries, and performance metrics to generate insights about which suppliers consistently meet delivery times, quality standards, and cost expectations.
- Action:
- Implement AI-based analytics within Acumatica’s Vendor Management module to evaluate supplier performance. Use this data to streamline your supplier selection process, optimize lead times, and potentially negotiate better contracts based on data-backed insights.
5. AI-Powered Inventory Audits and Cycle Counting
Conducting physical inventory audits or cycle counts is often time-consuming and prone to human error. AI can enhance the cycle counting process by analyzing historical data to predict when certain items are more likely to be out of place or incorrectly counted.
- How it works in Acumatica:
- AI can be used to predict inventory discrepancies by comparing actual stock levels with historical data, helping to identify potential areas for audit.
- The system can prioritize inventory counts for high-turnover items, items with a history of discrepancies, or critical products based on AI-driven risk assessments.
- Action:
- Use AI-powered cycle counting tools to automate inventory audits. Incorporate machine learning models that can suggest the frequency and focus areas for cycle counting within Acumatica.
- Implement RFID or barcode scanning technologies in conjunction with AI to track inventory and reduce human error in counting.
6. Predicting Stockouts and Overstock Situations
AI can help predict stockouts before they happen by analyzing trends such as customer demand, current inventory levels, and supplier performance. Similarly, AI can also identify products that are at risk of overstocking.
- How it works in Acumatica:
- By incorporating AI into Acumatica’s Inventory Management module, the system will use historical sales patterns, supplier lead times, and seasonality to predict when stock levels will drop below minimum thresholds.
- AI algorithms can automatically raise alerts or even trigger reordering processes when stock levels are predicted to hit critical levels.
- Action:
- Set up AI-driven alerts in Acumatica for items that are at risk of stockouts or overstocking.
- Use AI-powered recommendations for adjusting reorder points based on real-time data and predictive analytics.
7. AI-Powered Supplier and Demand Matching
AI can help match your suppliers with the right demand forecast and optimize order quantities to meet demand without over-ordering or under-ordering.
- How it works in Acumatica:
- By integrating AI-driven forecasting and supplier lead time data into Acumatica, AI can recommend the most efficient ordering strategy for each supplier, ensuring timely deliveries and optimal stock levels.
- Action:
- Enable automated supplier demand matching within Acumatica to ensure that inventory levels are always aligned with the most accurate forecasts.
8. AI for Identifying and Managing Slow-Moving Inventory
AI can help identify products that are slow-moving or dead stock, allowing businesses to take corrective actions like promotions or discounts to clear out stock.
- How it works in Acumatica:
- AI algorithms can track sales velocity and compare it against stock levels to identify products that are not selling as expected.
- The AI can generate reports on slow-moving items, propose sales strategies, or recommend liquidation methods to reduce excess inventory.
- Action:
- Set up AI-powered slow-moving inventory alerts within Acumatica and use the AI suggestions to make decisions about discounting, bundle offers, or removing items from your inventory.
Video: Report Creation in Acumatica (Platform video)
Is there an Acumatica Report that shows all Inventory?
Yes, Acumatica offers several reports that give a comprehensive overview of all inventory items across your entire system. Some of the most useful reports for showing all inventory include:
1. Inventory Item List
The Inventory Item List report is a basic yet effective report that shows all the inventory items in your system, along with key details such as item codes, descriptions, quantities on hand, and stock values. This report is helpful for a quick overview of your entire inventory.
2. Inventory Transactions Report
The Inventory Transactions Report shows all transactions that have affected inventory levels, including purchases, sales, transfers, and adjustments. This report provides a detailed view of inventory movement, which is essential for understanding inventory activity over a specific period.
3. Inventory Valuation Report
This report displays all inventory items and their corresponding values, based on your selected inventory valuation method. The report shows the total value of your stock, as well as how that value has changed over time, which is particularly useful for financial analysis.
4. Inventory Aging Report
The Inventory Aging Report categorizes inventory by the length of time it has been in stock. This report can help you identify slow-moving items that may need to be discounted, promoted, or removed from your inventory.
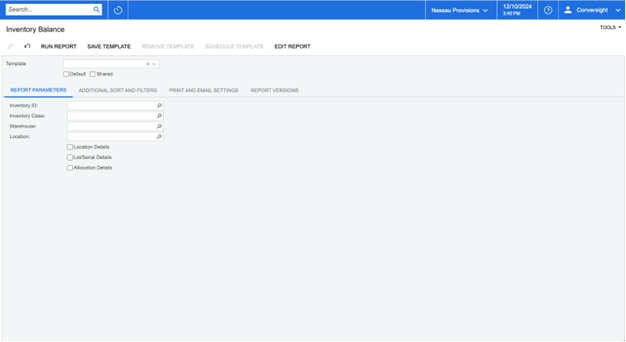
Automated Reporting with ConverSight
Automating inventory management in Acumatica with ConverSight can significantly enhance efficiency, streamline operations, and reduce human error. ConverSight, with its AI-powered analytics and integration capabilities, offers tools that can automate many aspects of inventory management in Acumatica, including stock tracking, demand forecasting, order management, and supplier coordination.
1. Integrate ConverSight with Acumatica
Before automating inventory management, ensure that ConverSight is properly integrated with Acumatica. This allows for real-time data exchange between the two systems, ensuring that inventory data, orders, sales, and other metrics are continuously updated.
- Action:
- Work with your IT team or Acumatica partner to establish an integration between Acumatica and ConverSight.
- Ensure that relevant data fields such as inventory levels, sales orders, purchase orders, and supplier data are synchronized.
2. Automate Inventory Forecasting and Demand Planning
AI-powered demand forecasting is one of the key features that ConverSight offers to automate inventory management. Using historical sales data and advanced machine learning models, ConverSight can predict future demand, allowing you to adjust stock levels proactively.
- Action:
- Configure ConverSight’s demand forecasting tool to analyze historical sales data and generate accurate demand predictions.
- Set up automated reorder points in Acumatica based on these predictions so that the system automatically places orders when stock levels reach a threshold.
- Adjust safety stock levels based on forecast data to avoid stockouts or overstocking.
Benefits:
- Accurate forecasts based on historical data, seasonality, and trends.
- Proactive inventory replenishment to reduce manual intervention.
3. Automate Stock Replenishment
Once you have forecasted demand, you can automate the process of stock replenishment. ConverSight can recommend when and how much inventory should be ordered based on real-time analytics.
- Action:
- Use ConverSight’s inventory recommendations to determine when to reorder stock based on demand forecasts and current inventory levels.
- Set up automated purchase orders in Acumatica that are triggered by low inventory or approaching stock-out conditions, based on ConverSight’s recommendations.
- Integrate lead time data for suppliers into the system to automate the replenishment process in a timely manner, ensuring inventory arrives when needed.
Benefits:
- Streamlined ordering process with less manual oversight.
- Reduced risk of stockouts or excess inventory.
4. AI-Powered Supplier Management and Coordination
ConverSight helps optimize supplier relationships by providing insights into supplier performance, delivery times, and order accuracy. By automating this process, you can ensure that you’re always working with the most reliable suppliers and minimize delays.
- Action:
- Analyze supplier data in ConverSight to understand supplier lead times, order fulfillment rates, and performance.
- Use this data to automatically select suppliers for reorder based on their reliability and performance history.
- Automate purchase orders based on the supplier’s lead time and product availability, ensuring timely restocking.
Benefits:
- Improved supplier relationships through data-driven insights.
- Reduced manual oversight of supplier management.
5. Automate Stock Adjustments Based on Real-Time Data
ConverSight can continuously analyze inventory movements in real-time, allowing the system to flag discrepancies or trends that require attention. By integrating this capability with Acumatica, stock adjustments can be automated.
- Action:
- Enable real-time inventory tracking in Acumatica via ConverSight to detect changes in inventory, including stockouts, excess stock, or discrepancies.
- Use AI-driven alerts in ConverSight to notify relevant stakeholders about stock levels that need attention, such as items that are moving too quickly or too slowly.
- Set up automated inventory adjustments in Acumatica, where the system can automatically adjust stock levels based on discrepancies detected by ConverSight.
Benefits:
- Continuous monitoring of inventory for stock discrepancies.
- Faster response times to address any issues or discrepancies.
6. Automate Inventory Reconciliation and Cycle Counting
AI-powered cycle counting and inventory reconciliation can be automated using ConverSight, ensuring that inventory counts are accurate without requiring manual intervention.
- Action:
- Use AI-based insights from ConverSight to prioritize high-value or high-turnover items for cycle counting.
- Set up automated alerts for discrepancies between physical inventory and recorded inventory, so that corrective actions can be taken promptly.
- Automate inventory counts and reconciliations in Acumatica, allowing cycle counts to trigger adjustments automatically.
Benefits:
- Reduced human error during inventory counts.
- Less time spent on manual reconciliation efforts.
7. Optimize Inventory Location and Warehouse Management
If your business operates in multiple locations or warehouses, ConverSight can automate inventory distribution between sites based on demand, stock levels, and warehouse capacity. This ensures efficient stock movement and utilization across the organization.
- Action:
- Use ConverSight’s AI-driven analytics to monitor inventory across multiple warehouses or locations.
- Automatically redistribute stock based on demand, ensuring that high-demand products are always available in the right locations.
- Set up automated stock transfers in Acumatica, triggered by ConverSight’s analysis of inventory levels across different sites.
Benefits:
- Optimized inventory levels across multiple locations.
- Improved warehouse efficiency through automated stock movement.
8. Automate Reporting and Analytics for Inventory Management
ConverSight provides real-time reporting and interactive dashboards that can be automated to generate insights about your inventory management. These reports can be scheduled and automatically sent to key stakeholders.
- Action:
- Set up automated reports in ConverSight that provide insights into key inventory metrics like stock turnover, aging inventory, order trends, and stockouts.
- Schedule these reports to be sent to managers, warehouse teams, and procurement teams at predefined intervals (e.g., daily, weekly, monthly).
- Use interactive dashboards that give stakeholders real-time access to inventory status and recommendations for adjustments.
Benefits:
- Timely, data-driven insights for decision-making.
- Less reliance on manual reporting and data entry.
9. Use ConverSight’s Natural Language Queries for Inventory Insights
One of the unique features of ConverSight is its ability to handle natural language queries, allowing users to ask questions about inventory status, trends, or predictions without needing technical expertise.
- Action:
- Train your team to use natural language queries to retrieve inventory reports quickly (e.g., “What is the current stock level for item X?” or “Which items have been overstocked in the last 30 days?”).
- Use AI-driven insights from these queries to automate restocking or reordering actions within Acumatica.
Benefits:
- Faster access to insights without complex data manipulation.
- Increased efficiency and better decision-making.
10. Implement AI-Powered Alerts for Proactive Inventory Management
Set up AI-driven alerts in ConverSight that notify relevant users when specific inventory thresholds are crossed or when anomalies are detected. This can be an important part of the automation process, as it ensures proactive action before problems arise.
- Action:
- Configure alerts for low stock, high stock, aging inventory, and unfulfilled orders based on AI insights.
- Set up rules for automated replenishment or stock movement based on these alerts.
Benefits:
- Proactive management of inventory.
- Reduced risk of stockouts, overstocking, and waste.
How to add Custom Fields to Inventory Lookup
Acumatica allows users to customize their inventory setup to meet specific business requirements. Adding custom fields to the inventory lookup screen is one such customization that can help businesses track additional information about their inventory items.
1. Navigate to the Customization Menu
To add custom fields, go to the “Customization” menu within Acumatica. From here, select “Customization Projects” to create or modify an existing project.
2. Create a New Customization Project
If you don’t already have a customization project, click “New Project.” Give it a name (e.g., “Inventory Custom Fields”) and select “Add” to start editing the inventory module.
3. Add a New Field to the Inventory Table
In the Customization Project editor, navigate to the Inventory table (usually named InventoryItem). From here, click “Add Field” to create a new custom field. You can choose from various data types (text, date, number, etc.) depending on the kind of information you wish to track.
4. Edit the Inventory Lookup Screen
Next, navigate to the Inventory Lookup screen, where you want the new custom field to appear. In the screen editor, select the area where you want to place the custom field, then drag and drop the newly created field into the desired location.
5. Publish the Customization
Once you’ve added the custom field to the lookup screen, save your changes, and publish the customization. The new field will now be visible on the Inventory Lookup screen, allowing users to enter and view additional data for each inventory item.
6. Testing the Custom Field
After publishing the customization, test the new field by adding data to it in the Inventory Lookup screen. Make sure it functions as expected and integrates with other areas of the system, such as reports or dashboards.
By adding custom fields to the Inventory Lookup screen, you can ensure that Acumatica is tailored to your unique business needs and provides all the information you require to manage
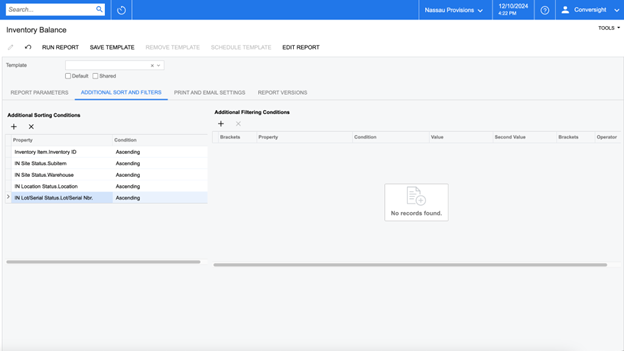
Adding AI-Powered Decision Intelligence to Acumatica
Some top use cases that customers are utilizing in ConverSight include:
- AI-Driven Demand Forecasting: One of the most impactful ways ConverSight can help is by improving demand forecasting. AI-based forecasting tools analyze historical sales data, seasonality, and external factors to predict future demand more accurately.
- ROI: 55% reduction in decision cycle time, 75% reduction in time spent by analysts, 28% reduction in stockouts
- Real-Time Inventory Tracking & Insights: ConverSight provides real-time visibility into your inventory across multiple locations, warehouses, or sales channels. This allows for more precise tracking of stock levels and performance metrics.
- ROI: 40% reduction in time spent creating reports, 18% increase in on-time delivery, 24% reduction in e-commerce order fulfillment costs
- Automate Stock Replenishment: ConverSight uses AI and predictive analytics to automate inventory replenishment based on real-time data and demand forecasts. This can significantly reduce manual oversight and streamline purchasing processes.
- ROI: 12% reduction in PO fulfillment delay, 40% reduction in PO and MO cycle time, 10% decrease in month-to-month costs
Conclusion
Integrating AI and automation from ConverSight into Acumatica ERP can greatly enhance its capabilities, transforming how businesses manage core operations such as inventory, finance, customer service, sales, and supply chain. By leveraging artificial intelligence and automation, Acumatica ERP becomes smarter, more efficient, and proactive in decision-making, allowing companies to stay competitive and agile. ConverSight provides a platform for easily integrating AI and automation into your Acumatica Cloud ERP instance, providing the most optimized and up-to-date insights.
See firsthand how ConverSight can revolutionize your Acumatica instance.